- -50%
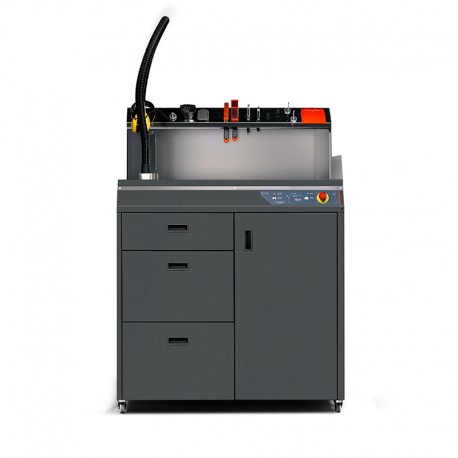
Sinterit is a Polish company recognized as a pioneer in SLS desktop printing. However, they not only offer the most affordable SLS 3D printers on the market, but also provide a complete ecosystem of dedicated peripherals to facilitate the entire workflow, from print preparation to post-processing of parts.
The Sinterit Powder Handling Station v2 powder handling system includes a larger powder hopper of up to 20 L, as well as a new operating interface that simplifies the workflow.
Sinterit Powder Handling Station v2 is a device designed to integrate with both Sinterit SLS 3D printers and the rest of the brand's peripherals. It is a powder handling station that connects to the ATEX vacuum cleaner and allows the printer to be placed on one side and the Sandblaster SLS booth on the other.
The PHS v2 has an internal sieving and cooling system with a capacity of up to 20 liters of powder, an area to keep the Dedicated Powder Tools components tidy and three distinct work areas: one dedicated to cleaning the printer and workspace, one dedicated to unpacking and powder recovery, and one dedicated to post-processing of the parts.
Thanks to the Powder Handling Station, the entire workflow is reduced to 5 convenient steps that can be performed in one place:
Once printing is complete, the block of dust is transferred directly to the surface of the PHS v2, where the excess dust falls through a grid where, thanks to the integration of the ATEX vacuum cleaner and the cyclone separator, it is separated and collected in a container.
Once the parts have been recovered from the dust block, they are passed on to the cleaning area, where they are cleaned with the help of the accessories included in the Dedicated Power Tools. The dust removed from the surface of the parts is recovered through a fine grid and collected in the same container where the dust recovered from the printing block was collected.
After cleaning the parts, these can be sandblasted into the Sandblaster or Sandblaster SLS for a perfect finish. Thanks to the built-in support, both the Sandblaster and the Sandblaster SLS can be placed next to the work surface, minimizing shifting.
Once the parts are ready, the printer and the surface of the PHS can be cleaned thanks to the integrated hose with interchangeable nozzles. Thanks to this the ATEX vacuum cleaner can remain fixed in one place. All the dust recovered from the cleaning is collected and separated, joining the recovered from the cleaning of the parts.
Finally, all the recovered powder, together with the necessary amount of soda, is added to the integrated sieve unit to obtain the powder ready for the next print.
The new Powder Handling Station v2 increases powder handling capacity to 20 L for improved compatibility with the Lisa X and NILS480 printers, as well as incorporating a new interface panel that improves workflow and allows control of the ATEX vacuum cleaner and Sandblaster.
General information |
|
Manufacturer | Sinterit |
Maximum sound level | < 60 dB |
Electrical properties |
|
Input | 110/230 V AC, 12 V DC 6.67 A |
Consumption | 80 W |
Dimensions and weight |
|
Dimensions | 700 x 1000 x 1580 mm |
Weight | 150 K g |
Package dimensions | 1200 x 800 x 1580 mm |
Package weight | 185 Kg |
Space required for installation | 1700 x 2200 x 1800 mm |
Other |
|
HS Code | 8477.8099 |
Manufacturer | Sinterit |
---|---|
Weight | 150 kg |
Dimensions | 700 x 1000 x 1580 |
Space required for installation | 1700 x 2200 x 1800 |
Power | 110/230 [V] AC, 12 VDC 6,67 A, 80W |
Content | |
Powder Handling Station | 1x Powder Handling Station |