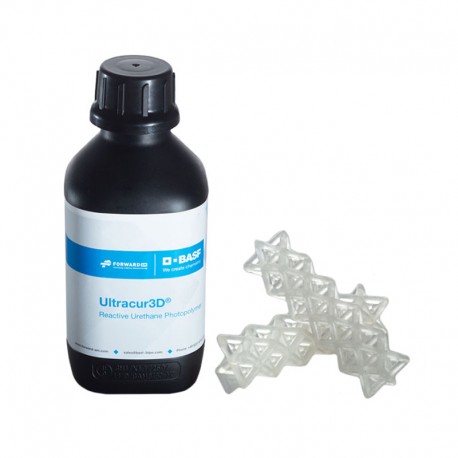
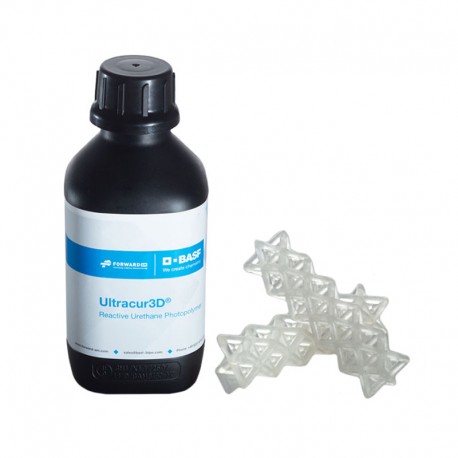
Ultracur FL60 is a cutting-edge reactive urethane photopolymer developed by BASF (Forward AM) as part of their Flexible resins portfolio. This material is specifically tailored for flexible applications, striking an impressive balance between flexibility and high tear strength. With a Shore hardness of 60 A, FL60 offers a soft, comfortable feel while ensuring robust performance for a variety of applications, making it an excellent choice for projects that demand both resilience and tactile quality.
The mechanical properties of Ultracur FL60 further emphasize its versatility and reliability. It features a notable elongation at break of 90%, allowing it to bend and stretch while maintaining its structural integrity. Additionally, with a tear strength of 9 N/mm and a rebound resilience of 11%, this resin is engineered to withstand dynamic conditions, making it particularly suitable for applications in footwear, functional prototyping, cushioning pads, and flexible grips. The long-term color stability of FL60 ensures that products maintain their aesthetic appeal over time, even in demanding environments.
Ultracur FL60 is compatible with a range of 3D printing technologies such as LCD/DLP/SLA, facilitating seamless integration into existing production workflows. Its adaptability allows it to be used with various printing methods, ensuring that users can achieve high-quality results across different projects. This makes FL60 an attractive option for manufacturers looking to streamline their processes while producing high-performance flexible components.
For those seeking comprehensive information about Ultracur FL60's capabilities, a detailed technical data sheet that covers crucial aspects such as UV resistance and sterilization is available in the Attachments section. The accompanying user manual serves as a practical guide on storage, printer settings, and post-processing techniques to optimize material use. To further enhance user experience, the BASF (Forward AM) settings navigator helps pinpoint suitable printer settings for specific equipment, ensuring successful print outcomes and maximizing the effectiveness of FL60 resin in diverse applications.
General information |
|
Manufacturer | BASF |
Material | Urethane-acrylate oligomers |
Format | 1 kg / 10 kg |
Technology | SLA / LED-LCD / DLP |
Wavelength | 385 / 405 nm |
Viscosity | @ 25 ºC: 50 mPas / @ 30 ºC 400 mPas |
Density (solid) | (ASTM D792) 1.16 g/cm³ |
Density (liquid) | (ASTM D4052-18a) 1.08 g/cm³ |
Printing properties |
|
Layer height | - µm |
Layer exposure time | - |
Layer off time | - |
Bottom layer exposure | - |
Bottom layer count | - |
Mechanical properties |
|
Izod impact strength | - KJ/m² |
Charpy impact strength | - KJ/m² |
Elongation at break | (ASTM D412C) 90 % |
Tensile strength | (ASTM D412C) 4 MPa |
Tensile modulus | - MPa |
Flexural strength | - MPa |
Flexural modulus | - MPa |
Surface hardness | (ASTM D2240) Shore 60 A |
Wear resistance | (ASTM D624-C, Graves) 9 kN/m / (ASTM D412-C, Trouser) 2 kN/m |
Resilience | (ASTM D7121) 11 % |
Compression | (ASTM D395-B @ 23 ºC, 72 h) 0 - 0.5 % |
Thermal properties |
|
Softening temperature | (ASTM D1525) 59 ºC |
Specific properties |
|
Maximum water absorption | (ASTM D570, 24 h) 1.26 % |
Curing, washing, and sintering properties |
|
Washing time | - |
Curing time | - |
Curing temperature | - ºC |
Other |
|
HS Code | 2916.1 |
Lifetime (since manufacturing) | 12 M |
The Ultracur3D resins from BASF exhibit high light sensitivity, so they should always be stored in their closed container and away from light.
Before starting a print, it is necessary to shake the resin well and, if possible, place it under vacuum to eliminate any bubbles that may have formed.
Once printed, the cleaning of the parts must be done with isopropyl alcohol. It is recommended to submerge the parts in a container with isopropyl alcohol and place this container inside an ultrasonic cleaner for 4 minutes. It is advisable not to immerse the part for extended periods to avoid deformation and softening.
After cleaning, the parts should dry for 30 minutes at 40 ºC. Once dry, the parts printed with BASF Ultracur3D resins should cure at room temperature to achieve optimal properties. The curing conditions will depend on the characteristics of the printer used and the curing equipment.