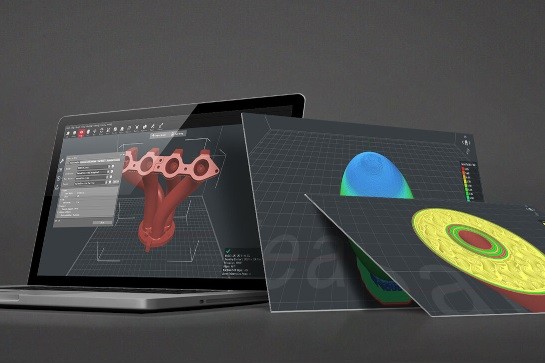
Lorsque vous préparez un fichier pour l'impression, il est très important de connaître les paramètres de base et leur fonctionnement. Le nombre de paramètres disponibles dans les logiciels de pelliculage d'aujourd'hui ne cesse d'augmenter. Toutefois, à moins d'avoir une connaissance approfondie du logiciel et de la technologie, il est conseillé de commencer par ne modifier que les paramètres de base.
On peut distinguer trois groupes de paramètres : ceux qui dépendent du matériau, ceux qui définissent le profil d'impression et ceux qui définissent le matériel. Selon le logiciel, ils peuvent apparaître dans différentes catégories ou être mélangés.
Paramètres définissant le hardware
Ils sont généralement liés à la buse de l'imprimante et doivent être modifiés lors du passage à une buse d'un diamètre différent.
-
Diamètre de la buse : Il s'agit du diamètre réel de la buse utilisée. Si une buse de 0.4 est utilisée, il faut choisir 0.4 mm.
- Largeur d'extrusion : Il s'agit de la largeur réelle de la ligne d'extrusion, elle dépend de la hauteur de couche utilisée et est généralement plus grande que le diamètre de la buse. Pour connaître la valeur réelle, il est nécessaire d'imprimer un cube en mode coupe et de mesurer l'épaisseur réelle de la paroi. Pour une hauteur de couche égale à 50% du diamètre de la buse, la largeur d'extrusion est généralement 20% plus grande. C'est-à-dire que si une buse de 0.4 mm et une hauteur de couche de 0.2 mm sont utilisées, la largeur d'extrusion sera de 0.48 mm.
Paramètres du matériau
Les paramètres des matériaux sont ceux qui dépendent directement de chaque matériau et qui doivent donc être modifiés lors du changement de matériau. Les plus importantes sont :
- Température d'impression : définit la température de la buse pendant l'impression. Il s'agit d'une donnée fournie par les fabricants, mais il est recommandé de la calibrer pour chaque imprimante.
- Température de base : comme pour la température d'impression, il faut consulter les informations du fabricant pour chaque matériau. Définit la température de la base pendant l'impression.
- Température de la chambre : disponible uniquement sur les imprimantes avec chambre chauffée. Définit la température de la chambre pendant l'impression. Une température légèrement inférieure à la Tg du matériau est généralement utilisée.
- Flux : Il s'agit d'un facteur de compensation de la vitesse d'extrusion relative à la vitesse d'impression. Une valeur inférieure à 1 (ou 100 %) entraîne une extrusion moindre, tandis qu'une valeur supérieure à 1 (ou 100 %) entraîne une extrusion excessive. Bien que la valeur correcte soit généralement de 1, certains matériaux tels que le PLA ou le PETg peuvent exiger des valeurs inférieures (0.9-0.95) tandis que d'autres exigent des valeurs supérieures, comme le TPE et le TPU (1.05-1.15).
- Taux de rétraction : avec la distance de rétraction, ils définissent les valeurs de rétraction du matériau. Ce paramètre est également très dépendant du type d'imprimante utilisé. Il doit être réglé correctement pour chaque combinaison support-imprimante. Il se situe généralement dans une fourchette de 20 à 40 mm/s.
- Distance de rétraction : C'est la distance à laquelle le filament est rétracté avant chaque déplacement. Comme la vitesse de rétraction, elle doit être réglée correctement pour chaque combinaison matériau-imprimante.
- Vitesse du ventilateur de refroidissement : définit la vitesse du ventilateur de la couche et donc le refroidissement de la pièce pendant l'impression. Consultez les informations du fabricant pour savoir si le matériau nécessite ou non cette fonction. Avec l'ABS, il est généralement toujours désactivé, tandis qu'avec le PLA, il est utilisé à la vitesse maximale à tout moment. D'autres matériaux comme le PETg ou l'ASA peuvent nécessiter l'utilisation du ventilateur d'enduction à basse vitesse (20-50%). En général, les logiciels de laminage permettent de sélectionner différentes vitesses à différentes hauteurs, car dans tous les cas, le ventilateur doit être éteint dans les premières couches pour assurer une bonne adhésion à la plate-forme.
Paramètres définissant le profil d'impression
Ce sont des paramètres qui vont définir la qualité, la finition et la résistance de la pièce finale. Ils ne dépendent pas directement du matériau, il n'est donc pas nécessaire de les ajuster pour chaque matériau. Ils peuvent être classés en plusieurs catégories selon l'élément qu'ils affectent.
Paramètres de la couche
-
Hauteur de la couche : définit l'épaisseur de chaque couche. Le point idéal coïncide généralement avec la moitié du diamètre de la buse. Par exemple, pour une buse de 0.4 mm, il sera de 0.2 mm, tandis que pour une buse de 0.6 mm, il sera de 0.3 mm. Les hauteurs de couche supérieures à 75 % du diamètre de la buse ne doivent jamais être utilisées.
- Hauteur de la première couche : Définit la hauteur de la première couche, qui est en contact avec la base. Elle peut être fixée à une valeur légèrement inférieure à la hauteur de la couche, afin d'améliorer l'adhérence à la base.
- Nombre de couches solides inférieures : Définit le nombre de couches denses à imprimer sur le fond de la pièce. Le nombre de couches solides inférieures multiplié par la hauteur de la couche définit l'épaisseur de la paroi de la pièce au fond de la pièce. Il est recommandé d'utiliser un nombre suffisant de couches pour obtenir des épaisseurs supérieures à 1 mm.
- Nombre de couches solides supérieures : Définit le nombre de couches denses à imprimer sur la partie supérieure de la pièce. Le nombre de couches solides inférieures multiplié par la hauteur de la couche définit l'épaisseur de la paroi de la pièce au sommet. Il est recommandé d'utiliser un nombre suffisant de couches pour obtenir des épaisseurs supérieures à 1 mm.
Paramètres du périmètre :
-
Nombre de périmètres : Définit le nombre de périmètres que la pièce aura. L'épaisseur de la paroi de la pièce sera le nombre de périmètres multiplié par la largeur de l'extrusion. Il est recommandé d'utiliser un nombre minimum permettant d'obtenir une épaisseur de paroi d'au moins 1 mm.
- Mode tasse : Il s'agit d'une fonction présente dans la plupart des logiciels. Lorsqu'il est activé, un seul périmètre sera imprimé en continu sur toute la pièce.
Image 1 : Pièce imprimée en mode coupe. Source : Prusaprinters
Paramètres de remplissage :
-
Densité de remplissage : C'est la proportion de remplissage à l'intérieur de la pièce. Elle est définie comme le volume occupé par le matériau par rapport au volume vide. Ainsi, avec une densité de remplissage de 50%, la moitié du volume interne de la pièce sera vide. Il est habituel d'utiliser des valeurs comprises entre 10 et 30%.
- Motif de remplissage : définit la géométrie du motif de remplissage. Tous les logiciels ne présentent pas les mêmes caractéristiques, mais on peut les classer en trois catégories :
-
Bi-dimensionnels ou planaires : ce sont les plus courants, tels que rectiligne, grille ou triangulaire. Ils sont généralement les plus rapides, mais produisent généralement une forte anisotropie de la pièce.
-
Tridimensionnel : tel que gyroïde ou cubique. Ils offrent une anisotropie moindre de la pièce, mais impliquent généralement des temps d'impression plus longs..
-
Concentriques : ils conviennent pour une flexibilité maximale des pièces flexibles. Dans les pièces rigides, ils permettent généralement d'obtenir de meilleures finitions, car il n'y a pas de chevauchement avec les périmètres, mais les propriétés mécaniques de la pièce seront minimales. Ils peuvent convenir aux modèles visuels et aux maquettes.
Image 2 : Différents modèles de remplissage. Source : Prusaprinters.org
-
Chevauchement du remplissage : Il s'agit de la distance à laquelle les lignes de remplissage se chevauchent sur les périmètres. Une valeur élevée améliore la résistance de la pièce, mais le motif de remplissage peut devenir visible à la surface de la pièce.
- Combiner le remplissage : il s'agit d'une fonction très utile pour réduire les temps d'impression lorsque des hauteurs de couche très faibles sont utilisées. Par exemple, lors d'une impression avec une hauteur de couche de 0.1 et une buse de 0.4, il est possible de combiner un remplissage toutes les trois couches, de sorte que les parois seront imprimées avec une hauteur de couche de 0.1 mm et le remplissage avec une hauteur de couche de 0.3 mm, ce qui réduit considérablement le temps d'impression sans affecter la finition de surface de la pièce.
Ces paramètres de base, associés à des réglages de vitesse corrects, à des ajouts à la base et à des réglages corrects du support, permettent d'obtenir des profils d'impression complets et efficaces.